Conform normelor Uniunii Europene de reducere a consumului de combustibili fosili, începând cu 1 ianuarie 2009, rafinăriile din România trebuie să adauge 5% bioetanol în compoziţia benzinei. La un consum anual de benzină de circa 5 milioane tone, necesarul de bioetanol în etapa actuală este de aproximativ 350 milioane litri pe an, respectiv o producție zilnică de 1 milion de litri. Pornind de la aceste premise, este de la sine înțeles că atingerea unor astfel de cifre în producție este imposibilă fără ajutorul sistemelor electronice de monitorizare și control, numite SCADA (Supervisory Control and Data Acquisition). Rolul acestor sisteme este acela de a crește fiabilitatea echipamentelor din producție și, în mod implicit, eficiența la nivel de fabrică.
În cadrul acestui articol vă prezentăm un caz real de implementare a unui sistem SCADA, beneficiarul fiind un important producător de bioetanol din România.
Cerințele beneficiarului au fost următoarele:
• Achiziția de date de la diferiţi senzori de temperatură, presiune și nivel;
• Control atât manual, cât și automat asupra vanelor prezente la nivelul instalației;
• Comandă manuală de Pornire/ Oprire a celor două perechi de pompe din cadrul sistemului, cu condiția ca pompele ce fac parte din aceeași pereche să nu poată fi pornite în același timp;
• Arhivarea datelor preluate de la senzori și din producție într-o bază de date pentru o perioadă determinată de timp;
• Implementarea de algoritmi pentru definirea comportamentală a unui controler PID;
• Utilizarea controlerului PID pentru menținerea unui nivel constant al presiunii în diferite puncte ale sistemului și al nivelului de lichid dintr-un rezervor;
• Vizualizarea grafică a evoluției în timp a parametrilor măsurați;
• Posibilitatea de a seta o limită inferioară și superioară pentru fiecare parametru în parte;
• Implementarea unui sistem de avertizare vizuală și acustică a operatorului cu privire la depășirea limitelor normale a anumitor parametri;
• Posibilitatea ca operatorul să poată anula aceste alarme în momentul remedierii problemelor ce le-au generat;
• Implementarea în cadrul aplicației software a unui configurator dedicat senzorilor și actuatorilor utilizați în sistem pentru a facilita înlocuirea rapidă a echipamentelor defecte.
Soluţie!
Pentru implementarea cu succes a acestui proiect am optat pentru un sistem format din: module de achiziție de date cu canale I/O atât analogice, cât și digitale; aplicație software dezvoltată sub LabVIEW; bază de date relațională, MySQL.
De ce LabVIEW?
Programul (software-ul) a fost realizat complet în mediul de programare LabVIEW. Posibilităţile de dezvoltare şi testare avansate, dar şi gestiunea eficientă a detectării şi a semnalizării erorilor de comunicaţie (prin portul RS-232), sunt principalele considerente privind alegerea mediului de programare mai sus menţionat.
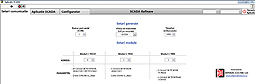
Cu un set complet de funcţii şi posibilităţi de implementare, atât pentru partea de control şi afişare destinată utilizatorului, cât şi pentru cea de automatizare, LabVIEW a fost utilizat pentru implementarea aplicației “SISTEM SCADA PENTRU SECŢIA DE RAFINĂRE”.
Pachetul software reprezintă interfaţarea modulelor de achiziţie de date cu calculatorul şi, implicit, cu utilizatorul. Prin intermediul acestei interfeţe utilizatorul poate seta parametrii de comunicaţie, de alarmă şi de calibrare a traductorilor folosiţi şi poate vizualiza atât istoricul evoluţiei acestor parametri pentru o perioadă de timp determinată, prin intermediul reprezentărilor grafice, cât și evoluția lor în timp real.
Prin intermediul aplicaţiei software se poate accesa o pagină dedicată exclusiv setărilor de comunicaţie cu modulele de achiziţie de date (DAQs), numită “Setări comunicaţie”.
Parametrii care se pot seta sunt: numărul portului COM, viteza de transmisie şi timeout-ul (aferente portului RS-232 de la PC), precum şi adresele modulelor DAQ.
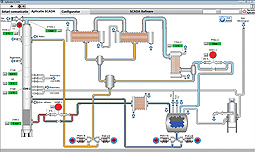
Valorile în timp real ale tuturor parametrilor, respectiv temperatură, presiune, nivel, stare vană, stare pompă, se pot vizualiza direct în pagina “Aplicaţie SCADA”. De asemenea, tot prin intermediul acestei pagini se pot accesa ferestrele de setare a limitelor de alarmă, a parametrilor PID şi a graficelor de evoluţie. Prin intermediul celei de-a treia pagini, numită “Configurator”, se setează parametrii senzorilor de temperatură şi a vanelor prin selectarea tipului de răspuns (4…20mA sau 0…20mA) şi prin setarea coeficienţilor ecuaţiei de conversie curent – mărime fizică (ex. temperatură, nivel etc.).
Descrierea interfeţei cu utilizatorul
Interfaţa cu utilizatorul constă într-un instrument virtual cu elemente grafice şi funcţionale. Butoanele virtuale, graficele şi indicatoarele numerice şi pseudo-analogice sunt conectate la sistemul de citire / scriere al comenzilor. În acest mod, pe ecran sunt afişate datele senzorilor, mesajele de eroare și alarmă, utilizatorul având acces la funcţiile de control asupra vanelor şi pompelor, disponibile prin intermediul modulelor DAQ atât cu ieşiri analogice în curent, cât şi cu ieşiri digitale cu relee. Interfaţa cu utilizatorul este ilustrată în figurile 1, 2 și 3. Cele trei pagini (tab-uri) se pot accesa independent prin comutaţie (vezi indicaţia din figura 3). Împărţirea afişării şi controlului sistemului în trei pagini este motivată prin necesitatea accesului facil la: gestiunea comunicaţiei (figura 1); panoul de monitorizare şi control al sistemului SCADA (figura 2); configurarea senzorilor şi vanelor (figura 3).
Fereastra de analiză detaliată a parametrilor monitorizaţi
În figura 4 este prezentată fereastra de analiză detaliată a parametrilor monitorizați – temperatură, nivel, presiune – în care s-a evidențiat elementul de reprezentare grafică și numerică în timp real. Prin intermediul acestei ferestre se afișează în timp real valoarea parametrului aferent, precum și limitele de alarmă. De asemenea, se poate observa zona de
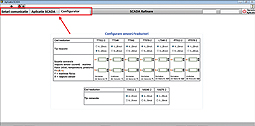
setare a limitelor de alarmă, atât limita inferioară, cât și cea superioară, precum și capătul de scală şi se pot defini culorile pentru fiecare zonă în parte.
O altă zonă de interes din acestă ferestră prezintă două elemente pentru monitorizarea stării de alarmă la nivelul parametrului în cauză (“STATUS”), precum și un buton de aprobare a alarmei (“Ack Alarm”). Martorul “STATUS” poate avea două stări: verde – valoare
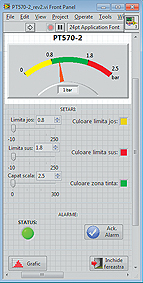
în limitele normale; roșu – valoare în afara limitelor normale – alarmă.
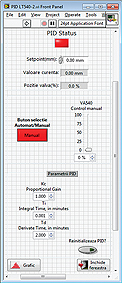
Cele două elemente din partea de jos a ferestrei reprezintă butoane la a căror acționare fie se deschide fereastra cu reprezentarea grafică cu evoluția parametrului aferent (“Grafic”), fie se închide fereastra curentă (“Închide fereastra”).
Fereastra de analiză și comandă a vanei
Elementele din figura 5 oferă utilizatorului posibilitatea de a selecta modul de control al vanei şi oferă indicii grafice pentru a arăta modul de operare al acesteia (roșu – manual, verde – automat PID).
Controlul manual este realizat prin intermediul slider-ului alăturat, iar cel automat, prin algoritm PID. În cazul utilizării algoritmului PID este necesară setarea următorilor parametri: setpoint, proportional gain, integral time și derivate time.
Prin acționarea butonului “Reiniţializează PID?” se resetează PID-ul prin setarea poziției vanei la starea inițială (0% sau 100%, după caz), reluând imediat algoritmul pentru atingerea și menținerea setpoint-ului. Acționarea butonului “Grafic” deschide fereastra cu reprezentarea grafică a evoluției parametrului aferent, iar butonul “Închide fereastra” închide fereastra curentă.
Fereastra grafic
În figura 6 este ilustrată fereastra de vizualizare grafică a datelor istorice.
În cadrul acesteia se pot analiza datele din producție din ultimele 72 de ore, date preluate de la senzorii de temperatură, presiune, nivel și de la vanele aferente. Se pot vizualiza concomitent evoluțiile presiunii și a vanei aferente, nivelului și a vanei aferente, precum și toate temperaturile.
În partea dreaptă din figura 6 este prezentată fereastra cursorului, prin intermediul căruia se pot vizualiza valorile instantanee ale parametrilor reprezentați grafic, la un anumit moment de timp. Cursorul se deplasează cu ajutorul mouse-ului.
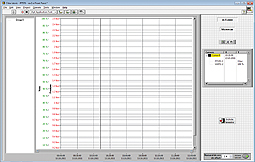
O opțiune importantă oferită în cadrul acestei ferestre este setarea perioadei pentru care se dorește vizualizarea datelor. Astfel, se poate alege de la 1 oră, până la 72 de ore, cu pas de 1 oră.
Concluzii
Sistemele SCADA aduc un plus important de fiabilitate și productivitate la nivelul fabricilor din orice tip de industrie, oferind atât operatorilor, cât și inginerilor de proces sau chiar a managerilor, o imagine reală asupra tuturor echipamentelor din producție. Vizualizarea valorilor din producție atât în timp real, cât și din trecut, ajută la creșterea vitezei și a calității la nivel decizional, oferind operatorilor un instrument de nădejde în îndeplinirea sarcinilor zilnice.
Prin implementarea unor algoritmi de alarmare instantanee pentru depășirea valorilor normale a parametrilor din producție se crește fiabilitatea și eficiența echipamentelor fabricii, operatorii putând evita în timp util defecțiuni ce ar putea duce la oprirea producției.
De asemenea, soluția prezentată oferă operatorului posibilitatea de a înlocui “din mers” elemente ce se pot defecta (senzori, traductori, actuatori etc).
Ing. Alexandru Marinică, MSc.
Inginer de Aplicații
Imperial Electric S.A.
Tel.: +40213240414
Fax: +40213240417
www.imperialelectric.ro
Ce este PID?
*PID = proportional–integral–derivative controller; mecanism de control cu buclă de reacţie utilizat cu precădere în sistemele de control industriale; calculează valoarea erorii ca fiind diferenţa dintre valoarea măsurată a variabilei de proces și valoarea ţintă; controlerul încearcă să minimizeze această eroare prin modificarea parametrilor de intrare ai procesului de control.